Ionization can be used in different fields for varied applications.
Our activities
The functions
Sterilize
Crosslink
Areas of application
Sterilization of single-use medical-surgical equipment and laboratory items is done through sealed packaging, at the stage of the product palletized.
It leaves no toxic residue in the ionized materials and therefore allows immediate use of the equipment after sterilization.
Recognized for its effectiveness since the early 1950s, ionization is the leading sterilization process in economically developed countries.
L’ionisation s’applique aux emballages vides, aux matières premières, mais aussi aux produits finis.
Elle s’inscrit dans le concept de l’assurance qualité au même titre que les procédés sous flux laminaires, les opérations en salles propres et l’automatisation des processus.
Ionization improves the mechanical properties of polyethylene films and allows, with equal performance, to reduce thicknesses by 40 to 60%.
It widens the melting ranges of shrink films. As a result, machine settings are less delicate and the quality of shrinkage is better.
Several research programs are underway to expand the range of applications for polymer ionization.
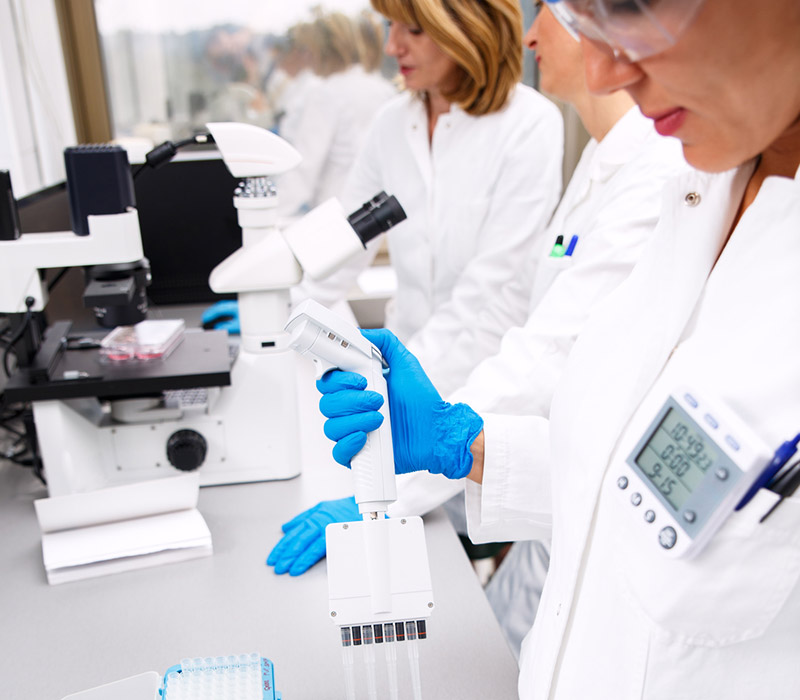
Techniques
The Ionisos group offers you the opportunity to jointly conduct research and development programs.
To complement its sterilization activity for medical equipment, cosmetic products, pharmaceutical raw materials, packaging… several associated services can be organized by the Ionisos group:
- consulting,
- information on legislation,
- transport and order splitting from our factories,
- refrigerated storage,
- microbiological testing.
- strength testing,
- process validation,
- performance qualification: beta process, gamma process, ethylene oxide
- training of your staff on our technologies.
For each treatment the IONISOS group performs:
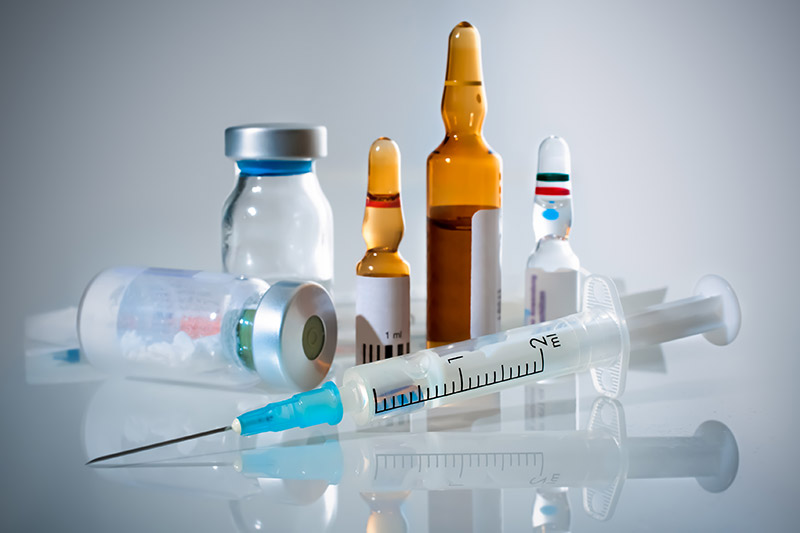
- computerized process control ensuring reliability, monitoring, and reproducibility,
- dose control according to applicable rules and regulations,
- documentary follow-up: issuance of a treatment certificate.